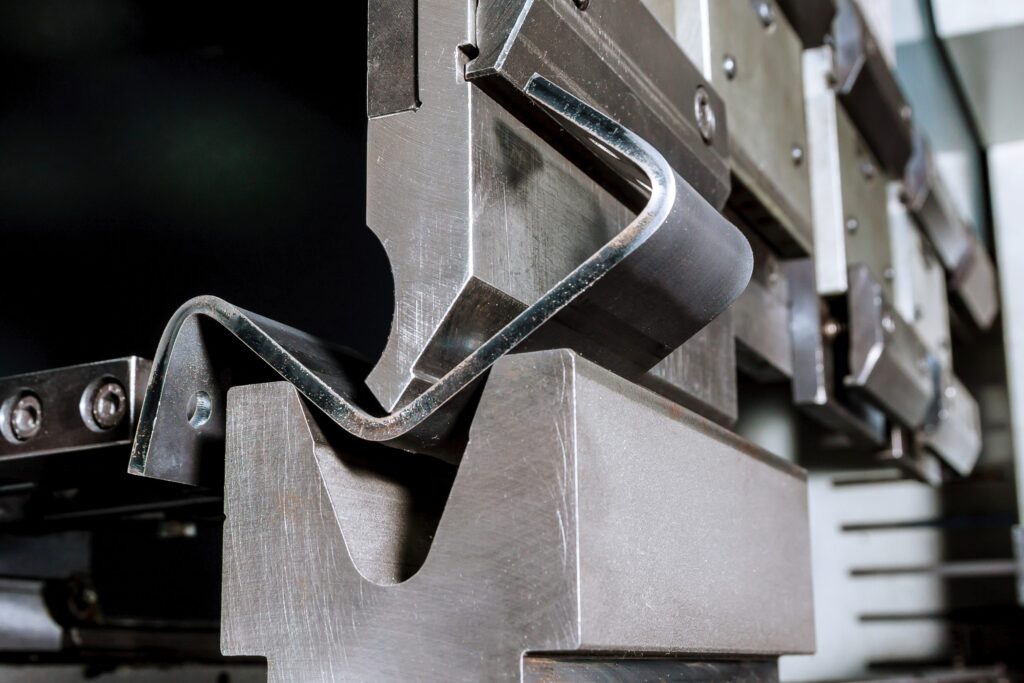
Source: benmachine.com
When we think of manufacturing, we often think of large factories with lots of machinery. But this isn’t always the case. In fact, oftentimes small businesses that use a lot of metal fabricating can be just as productive as their larger counterparts. This is thanks to the process behind metal fabrication, which is essentially a series of steps that are put into motion to create a product. In this blog post, we will explore the process behind metal fabrication and how you can use it to your advantage when building your business. We’ll also provide tips on how to optimize the process for maximum efficiency and yield.
What is Sheet Metal Fabrication?
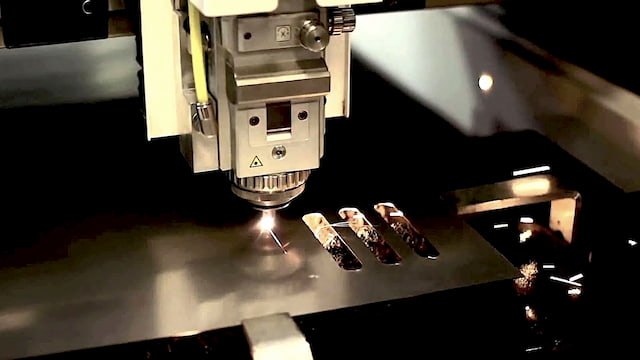
In sheet metal fabrication, a variety of processes are used to create products from metal sheets. The most common process is cutting and bending, which is how the metal is configured into the final product. Other processes include die casting, stamping, and forging. Each has its own set of advantages and disadvantages, so it’s important to choose the right one for the job at hand.
When choosing a sheet metal fabrication process, it’s important to consider the type of product you’re trying to create. Die cutting is good for creating complex shapes out of metal, while stamping is better for simple designs. Forging is perfect for creating heavy objects out of thin metal sheets.
Another factor to consider is the quality of the finished product. Different processes produce different levels of quality in the end product. For example, die cutting can result in rougher edges than stamping or forging, but it can also create more complex shapes that are harder to produce with other methods.
Ultimately, it’s important to test out different fabrication processes and see which ones are best suited for the specific project you’re working on.
The Different Types of Sheet Metal
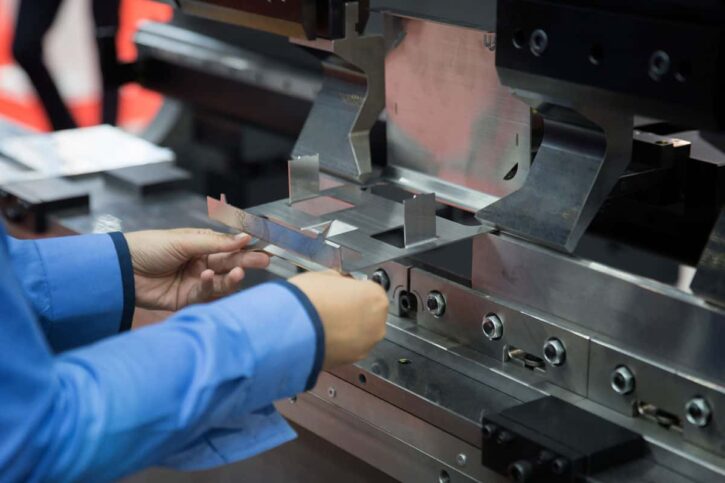
There are a few different types of sheet metal that can be fabricated, depending on the needs of the project. The most common type is hot rolled steel, which is simply steel that has been heated to a high temperature and then rolled into sheets. It’s the cheapest option and has a good range of properties, making it versatile for many purposes.
Cold rolled steel is slightly more expensive but has better flexibility and strength than hot rolled steel. It also has a rougher surface than hot rolled steel, which makes it better suited for applications where durability isn’t as important. Coiled tubing is a type of metal that’s made by winding iron or other metals around a central core. This process creates tubes with several different diameters that can be used in many different ways, including heating and cooling ductwork, electrical cables, and air conditioning units.
What to Expect when You Have a Service Call for Sheeting?
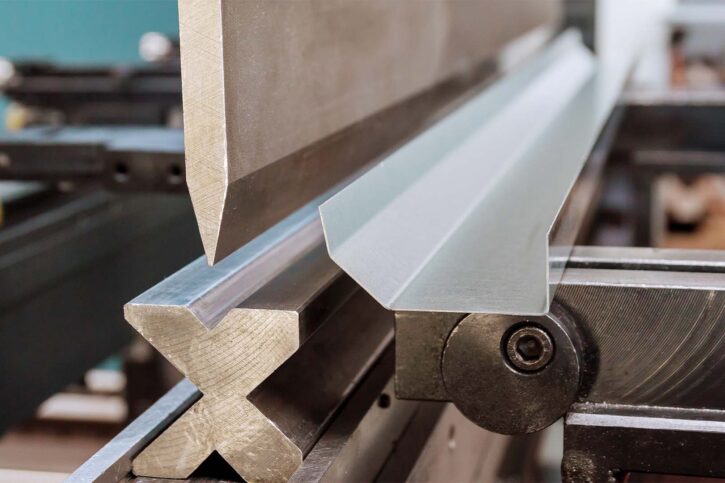
When you have a service call for sheet metal fabrication, expect the technician to arrive promptly and conduct a preliminary inspection of your job site. They will then provide an estimate of the time needed to complete the project. Be prepared to answer any questions the technician has about your project, and make sure to provide all pertinent information such as dimensions and specifications. The technician will also advise you on any necessary safety precautions that need to be taken during the fabrication process.
Once the work begins, you should expect regular updates from the technician so that you are always aware of the progress. In addition, be prepared to provide any additional input or clarifications that may be needed. When the job is completed, take a moment to inspect the final product for any irregularities or discrepancies. If there are any issues with your order, please let us know so that we can correct them quickly.
We hope that this information will help you understand the steps involved in fabricating a piece of metalworking equipment, and that it will give you a better understanding of what goes into creating a quality product.
Read this article.